
bluemonster1
LIFE MEMBER ONLY ONCE!!!
I decided to get going on making a device to remove the clutch sheaves.Seen some pics of how others have done so.The base is very strong and secure to hold the spider.The platform it is mounted to will be bolted down to a workbench so it is solid.I took 2 L-shaped angle iron,made a template of the mounting holes and transferred it to the plates.Once bolted down to the back of clutch,a long steel bar will drop in between the 2 plates snuggly and then I can twist the spider off.In my pics I just lay the bar in place and put a spacer above it and clamped it for now.I don;t have any bolts yet to mount to the clutch.Does anyone know what SIZE them BOLTS should be,I have to pick some up next week,they are fine thread to.
I know I,ll have to pre heat around the threads with a propane torch,but how much heat does it need to release.Is there any chance of wrecking the aluminum with a propane torch.Probably not!!!I will have to read up and confirm the right direction to twist off,clockwise I think looking from the backside.Will practice on my spare clutch first that I picked up from Turk.
Also I imagine this operation should be done on a fairly warm day,above 70.Wouldn;t want to try it when the aluminum is cold for fear of a crack.When I spin the pieces back on,I am to put a little loctite on the end of the threads,red loctite should do I assume.
I know I,ll have to pre heat around the threads with a propane torch,but how much heat does it need to release.Is there any chance of wrecking the aluminum with a propane torch.Probably not!!!I will have to read up and confirm the right direction to twist off,clockwise I think looking from the backside.Will practice on my spare clutch first that I picked up from Turk.
Also I imagine this operation should be done on a fairly warm day,above 70.Wouldn;t want to try it when the aluminum is cold for fear of a crack.When I spin the pieces back on,I am to put a little loctite on the end of the threads,red loctite should do I assume.
Attachments
2001SRX=Fast
New member
u got to much time on ur hands.

bluemonster1
LIFE MEMBER ONLY ONCE!!!
he`s alive..wow.Long time no see.Yep got 4 days off and the weather is the pits,so catch up on these things.Still working at CN.

bluemonster1
LIFE MEMBER ONLY ONCE!!!
hmmmm!!!!
Somebody must have a clue what size them bolts have to be to fit the threaded 6 holes on the backside of the primary.Is it a metric size you think.Can't find anything here at home that will fit them.Can't take the whole clutch with me to the hardware store to try diffrent bolts...LOL
Somebody ..please..somebody.......anybody find me.....some bolts .....that .....fit. Maybe daman would know.
Somebody must have a clue what size them bolts have to be to fit the threaded 6 holes on the backside of the primary.Is it a metric size you think.Can't find anything here at home that will fit them.Can't take the whole clutch with me to the hardware store to try diffrent bolts...LOL
Somebody ..please..somebody.......anybody find me.....some bolts .....that .....fit. Maybe daman would know.

bluemonster1
LIFE MEMBER ONLY ONCE!!!
Well............................What you think!!!!
Well its a brand new day.Anyone maybe know the exact thread size and/or bolt size for the back of primary?
Well its a brand new day.Anyone maybe know the exact thread size and/or bolt size for the back of primary?
bluewho
Active member
Well i see you are a carpenter//
///////////////
//?
///////////////
//?

bluemonster1
LIFE MEMBER ONLY ONCE!!!
yup!!!!!nail nail bang bang cut cut!!!!!!
yep..just like Jesus..lol.Yes I enjoy woodworking and building things.Also like small mechanics to..got most of the tools that you'll ever need.I buy tools non stop,even if I use the tool only once..it saved me. It's a shame that when I pass on in this life that I have no son to pass these tools on to.Don't think my 2 daughters will have any use for them.
yep..just like Jesus..lol.Yes I enjoy woodworking and building things.Also like small mechanics to..got most of the tools that you'll ever need.I buy tools non stop,even if I use the tool only once..it saved me. It's a shame that when I pass on in this life that I have no son to pass these tools on to.Don't think my 2 daughters will have any use for them.
just use steel round stock and put it in the non threaded holes.

bluemonster1
LIFE MEMBER ONLY ONCE!!!
pro..I get what you mean,but don't have a way to weld the stock onto a plate.Probably could use bolts and nuts and let the bolt drop down lower then the nut into them holes.But I am using 2 angle plates with a bar in between that I can slide in or out or more leverage.I already have the 6 holes drilled in the angle iron.I'll just look for them correct bolts..not in a rush since there is no snow for at least 7 months.
bluemonster1 said:Somebody must have a clue what size them bolts have to be to fit the threaded 6 holes on the backside of the primary.Is it a metric size you think.Can't find anything here at home that will fit them.Can't take the whole clutch with me to the hardware store to try diffrent bolts...LOL
Somebody ..please..somebody.......anybody find me.....some bolts .....that .....fit. Maybe daman would know.
Bolts that fit those holes are 8mm x 1.0 pitch.

bluemonster1
LIFE MEMBER ONLY ONCE!!!
I hope that is correct because I'll pick some up this week.I was going to take a guess they were about 9 mm,off 1 mm.Thanks there fourbarrel. imagine your snow is all gone now to.
This thread can be deleted after I get them bolts..thanks again.
This thread can be deleted after I get them bolts..thanks again.

bluemonster1
LIFE MEMBER ONLY ONCE!!!
seems like the metric thread bolts come in numbers 2 apart.Like M6.M8,M10 etc. The M8 does have a 1.0 pitch in the charts I looked at.
Last edited:
bluemonster1 said:I hope that is correct because I'll pick some up this week.I was going to take a guess they were about 9 mm,off 1 mm.Thanks there fourbarrel. imagine your snow is all gone now to.
This thread can be deleted after I get them bolts..thanks again.
No prob on the bolts I had the sheave off mine and some bolts I bought a few years ago just had to correctly size them.Our snow has been gone for about 3 weeks or so now I'm actually trying to find some time in the next couple of days to summerize the sled and put it away for the summer.

bluemonster1
LIFE MEMBER ONLY ONCE!!!
Hey Thanks again fourbarrel,got them metric bolts and they fit.Will try and separate sheaves this weekend.
Now with the clutch sitting upside down in my jig with the inner back of sheave facing up is it correct to spin the sheave clockwise with the bar.I know I have to heat the area with a propane torch,how long do I have to heat and will the heat damage the aluminum if left there to long.I will put a couple of marks first on the sheave and shaft so that when I tighten back up I will align the marks up again.I will then use a little Red Loctite on a few of the threads also,but not over do it.Thanks.
Now with the clutch sitting upside down in my jig with the inner back of sheave facing up is it correct to spin the sheave clockwise with the bar.I know I have to heat the area with a propane torch,how long do I have to heat and will the heat damage the aluminum if left there to long.I will put a couple of marks first on the sheave and shaft so that when I tighten back up I will align the marks up again.I will then use a little Red Loctite on a few of the threads also,but not over do it.Thanks.
A little heat is all that should be requires as all you need to do is soften any loctite that was there but as far as damaging the aluminum I don't think a propane torch would give off enough heat to do that.
The threads are left hand so I think your correct there in turning it clockwise as it's upside down and as far as marking it to line them up again when you put it back together I wouldn't worry about that it's the torque that you need to apply to get the sheave tight on the shaft.If I remember correctly the torque on that is like 145-150 ft-lbs;basically all you do is when your tightening it back up is put a bit of loctite on the threads and give it all your worth until you think it's tight.
The threads are left hand so I think your correct there in turning it clockwise as it's upside down and as far as marking it to line them up again when you put it back together I wouldn't worry about that it's the torque that you need to apply to get the sheave tight on the shaft.If I remember correctly the torque on that is like 145-150 ft-lbs;basically all you do is when your tightening it back up is put a bit of loctite on the threads and give it all your worth until you think it's tight.


bluemonster1
LIFE MEMBER ONLY ONCE!!!
good enough then,I'll give it a twirl and let you know how it goes then.Will mount my jig on my work table in the garage and give her.The first time probably I will be a little careful and play it on the safe side.If it comes apart easy then I will do the other 2 clutches at the same time and get it all done at the same time.Thanks again.Wish me luck.

bluemonster1
LIFE MEMBER ONLY ONCE!!!
Well guys,it ain't that difficult after all to separate the sheaves and remove the spider.Took a little bit of grunt to turn the damn thing,with heat of course and a long rod 6' long,it started to undo itself.BINGO!!!!Got everything apart,changed main bushing with out a hassle,replace all 6 sliders with new.The only thing that gave me a problem was once I removed the primary cover bushing,I destroyed the new one putting it back in.Is that one ever tight or what!!!Only got 3/4 way in and damaged the edge and that was it.Was difficult to get back out.Found a better tool to pound that little sucker in.Sprayed with some silicone spray to help aid the process.Finally got it.So one clutch is done.When I screw the sheave back on,I will use a little red loctite on the end of the threads.When I spin it back on,how do I know how far it will go,will it stop at a certain point or do I just make sure the threads stay flush with back of the sheave where it threads into???Everything certainly feels snugger now with less play for sure.
The cover bushing I wrecked,I took it to the grinder and grinded off the side until the damage was gone.Instead of being 11/16" deep,it is now 9/16" deep and I should still be able to use it one one cover..right.
Here's a pic.I sprayed all components with liquid graphite also to keep things clean looking,but didn't spray the sheaves of course.
The cover bushing I wrecked,I took it to the grinder and grinded off the side until the damage was gone.Instead of being 11/16" deep,it is now 9/16" deep and I should still be able to use it one one cover..right.
Here's a pic.I sprayed all components with liquid graphite also to keep things clean looking,but didn't spray the sheaves of course.
Attachments
Last edited:

bluemonster1
LIFE MEMBER ONLY ONCE!!!
I figured it out anyways.When you screw the sheave onto the spider,there is a retainer grove where two half moon retainer rings slide into as a stop.Then you torgue it out from there.I made 2 marks on the threaded end and back sheave prior to removal.When I screw things tight by hand and the retainer rings are contacted,I have about 3/8" to twist to line up the marks.This will also represent my torgue spec because it will take a good grunt to spin the sheave that 3/8" to my mark.I am now all set.Great to learn new things.You guys can do it to,no need to go to the dealer like I did a fews years back and they charged me a good price for the whole procedure and replacement parts.Power to the rider.
and money saved to.
I will from now on every summer change the bushings and slides to make sure clutch is always running at peak..Also changing the bushings in the weights also.Eliminate play in the clutch and there is one less problem to worry about.
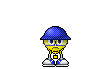



I will from now on every summer change the bushings and slides to make sure clutch is always running at peak..Also changing the bushings in the weights also.Eliminate play in the clutch and there is one less problem to worry about.
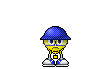
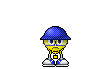
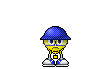

bluemonster1
LIFE MEMBER ONLY ONCE!!!
well got another clutch done complete today.New bushings thru out,weight bushings also,new washers and new slides and everything cleaned up good to.Tomorrow will finish up with the third primary clutch and then I will switch and change bushings on sheave and helix, and shoe ramps on my 2 secondaries.Clutches will be taken care of early before the next riding season.Will have to tackle my jackshaft later on.Got 2 jackshafts coming my way by next week.Another FUN project.






